3 highlights from the inaugural in-person Construction Technology Summit
Curated and organised by KHL Group and its publications – Construction Europe, Construction Technology, and International Construction – it was the first ConTech held in-person as construction industry leaders converged to hear about the world’s dynamic tech solutions shaping products and projects.
From automation and electrification to building information modelling (BIM) and digital/virtual twins to insight on the tech driving one of Saudi Arabia’s ‘US$500 billion’ Neom projects, here’s three highlights from ConTech’s first-ever in-person summit.
1) BIM and virtual twins saving Neom money on marketing
Joining ConTech remotely from Saudi Arabia was Paul Surin, head of digital & IT at Neom’s Trojena ski-resort project. As part of his programme, he navigated the immense digital renderings and BIM-supported software used on the Neom Trojena project.
Located in the far northwest corner of the country and situated at an elevation from 1,500m to 2,600m (4,921 ft to 8,530 ft) the project rests on 60km2 (20 sq mi) of mountainous terrain and has plans to include lodgings, ski runs, a wildlife reserve, and a manmade lake.
It’s expected to open to tourists in 2026 and host the 2029 Asian Winter Games.
Trojena is just one of 15 announced projects for the Neom, which will be a new urban area running across 26,500 km2 (10,200 sq mi) in the province of Tabuk, Saudi Arabia.
Surin illustrated how the sprawling futuristic-looking build – just this portion, he estimated, will cost more than $100 billion – is using present-day tech for both the build and marketing.
While discussing the scheme, videos of the project’s purpose-built digital user interface (UI), geographic information system (GIS) mapping, and a virtual or digital twin displayed the utilities of comprehensive modelling for a megaproject like Trojena.
“I managed to save an enormous amount of money on marketing, generating marketing content for videos, because we have the assets,” said Surin about the project modelling technology Neom is using. “There’s many users from sales and marketing down to construction [and] project operations.”
BIM practices implemented at the early stage of developing a digital or virtual twin for the project means the video-game-like graphics also include vital information on the necessities of the build; made accessible by gathering multiple datapoints.
“[We] also bring in things like live CCTV footage,” he explained.
Drone footage, too, combined with Oracle’s P6 portfolio management software and their Aconex construction project software aid the creation of the functional digital representative. Point-cloud scanning was also used to create the 4D render.
Combined altogether, contractors and workers have a polished full-scale render of Trojena, completed with build data, that can be accessed throughout construction.
“[It’s] an example of how, if you combine different data sets and you clean up the models, [you] can present the project in a different way,” said Surin. “It makes a big difference. We used it for presentations [with] different contractors, and it helps them understand where things are.”
On a scheme that is measured in square kilometres with more than 1,000 subcontractors, everyone working from a singular, digital source is vital, said Surin.
Ultimately, to achieve the country’s ambitious goals, efficiency and collaboration will be paramount.
“The price is massive,” he said. Reports estimated the entire Neom project could cost $500 billion, which means utilising BIM and digital twin technology to offset marketing costs is also financially prudent for the ambitious build.
“It’s all about the efficiency, sustainability, [and] looking at innovation,” Surin added. “Without the data and the solid foundation data, which need to be secured, we won’t be able to achieve much, and we will basically just have nice pictures, nice images, and nice videos.”
To push the technological advancement forward, deeper cooperation will go a long way, he said:
“[We’re] collaborating with different stakeholders, ecosystems, and visiting conferences, like this one, and talking to others and sharing knowledge, lessons-learned [and] breaking-up the old ways of thinking.”
2) Using 4D-planning, ITER project is closer to creating an ‘artificial Sun’
Laure Navarro, senior project manager for the ITER (International Thermonuclear Experimental Reactor) megaproject, was in Austin to discuss the goal of creating energy through a fusion process, which would create an artificial Sun in the south of France.
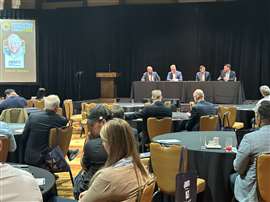
ITER is an international research and engineering scheme based in Saint-Paul-lès-Durance, with member countries China, India, Japan, Russia, South Korean, the US, Switzerland, and the UK, as well as the European Union, combining resources to create the ‘world’s largest’ experimental tokamak nuclear fusion reactor.
The reactor will heat plasma to 150-million-degrees Celsius (270-million-degrees Fahrenheit), which is a temperature approximately ten-times higher than the core of the Sun.
Navarro explained in simplest terms the complicated process.
“Fusion exists everywhere in the universe,” she said. “It’s the energy source of the Sun and the stars. In space, this is induced by gravitational forces. When we try to recreate that on earth, we need magnetic confinement fusion.”
The ‘tokamak’ is the term for the doughnut-shaped nuclear reactor that uses plasma and magnets – magnetic confinement fusion – to fuse hydrogen molecules to generate energy.
The entire ITER campus is on a 180-hectare site in the south of France. The project, including the 23,000-tonne (46,000-lb) tokamak, will cost US$20 billion, Navarro estimated, with construction to conclude in 2025.
The project relied on photogrammetry software and 4D-planning, a process of combining information-model components with scheduling information inside a 3D space. Photogrammetry is a method of creating a 3D representation with cameras, as opposed to scanners.
Utilising the combination of scanning technology, cameras, drones, and virtual reality augmentation, the ITER team was able to map out a functional model of the tokamak, which is used in the construction process.
Much like Surin noted on the Neom project, Navarro said these 4D interpretations are an aid to the communication and marketing teams.
“But we also use [it] for real planning work and sequencing work,” she said, showing a render of the reactor installation. “Remember that we have never built such a large tokamak in the world, and remember that every piece, no matter how small it looks, weighs hundreds of kilos.
“We really have to be really careful how we assemble things in what order, and we need to make sure that we can still continue assembling things without blocking our way,” she continued. “We do all this with 4D-planning on a weekly basis [and] this is shared with all the stakeholders, the construction managers, the schedulers, and we can get very good feedback to validate the sequencing before it’s actually done.”
Navarro showed how 4D-planning was used on a component assembly hall. Within the project model, the parts are placed digitally and the software identifies ahead of time where issues might arise.
“Here, we are validating the sequence and making sure that – by bringing components that are massive in size – we are not blocking the next steps,” she said. “We identify clashes in the sequence, and we validate the space available in the assembly hall.”
She said the 4D strategy helps optimise the site’s limited space and improves coordination between project stakeholders.
3) Hands-on experiences with new tech aid adoption
One of the biggest hurdles in moving the construction industry quicker toward automation, electrification, and remote operation can be contractor and operator uncertainty about the products.
Joel Honeyman, VP of global innovation for Doosan Bobcat, said consumers can be untrusting and even fearful regarding cost, productivity, and health and safety.
He noted that hands-on experiences with new tech can be instrumental in flipping the script.
With an exercise rooted in psychology, Honeywell illustrated how general perceptions are changing (and can be changed) on electric machines and novel tech.
“New technologies… some people like them, and some people don’t,” he acknowledged.
Honeywell played a video of a social experiment wherein contractors opposed to electric machines were given the opportunity by Doosan Bobcat to drive its latest model, the T7X– the ‘world’s first’ all-electric compact track loader.
However, the machine was disguised as an older model to help tamp down any potential bias from the operators. The video showed those operators lauding the machine’s power and ability.
“Their perceptions changed in ten minutes,” said Honeywell of the experiment. “They walked in our building a bunch of sceptics, [and] they walked out… believers.”
Providing a unique hands-on experience at ConTech was the world’s largest OEM, Caterpillar, which allowed event delegates the opportunity to remote-pilot in real-time a skid steer located in North Carolina, US – approximately 2,092-km (1,300-mi) east of Austin.
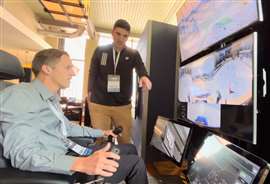
Using the Cat Command brand ‘Command Station’, ConTech demo operators were guided through navigating the training site, which included moving and picking up materials.
With the Command Station, operators can work in off-site locations from across the country utilising a simulated cab with joystick operation and digital read-outs.
“It gives the customer the opportunity to remove the operator from a potentially unsafe situation,” said Matt Magness, Caterpillar technology specialist, adding a single operator could also do more remotely.
While the demonstration at ConTech had the appearance of a large video game, Todd Farmer, product manager of construction digital and technology for Caterpillar, emphasised it is not for play.
“This is real. You can buy this today,” said Farmer, who noted the company has a consistent level of orders.
With “awareness and time”, Farmer said he believes remote operation like Cat Command will be commonplace on job sites.
He noted demonstrating the capabilities of Cat Command – like they did at ConTech – can help “change a [contractor’s] mindset on how they want to use technology.”
And some have fully embraced it already.
“We have customers that use it for their entire day of operation,” he said.
Check back for more coverage from the 2024 Construction Technology Summit.